Pressure transducers often play a critical role in underwater applications, where precise pressure measurement ensures equipment reliability, safety, and performance. For many underwater applications, these sensors must withstand extreme conditions – which are not limited to high pressures, but other variables as well, such as temperature variations and corrosive environments. Selecting the right pressure transducer for any given underwater application, therefore, requires the careful consideration of many factors.
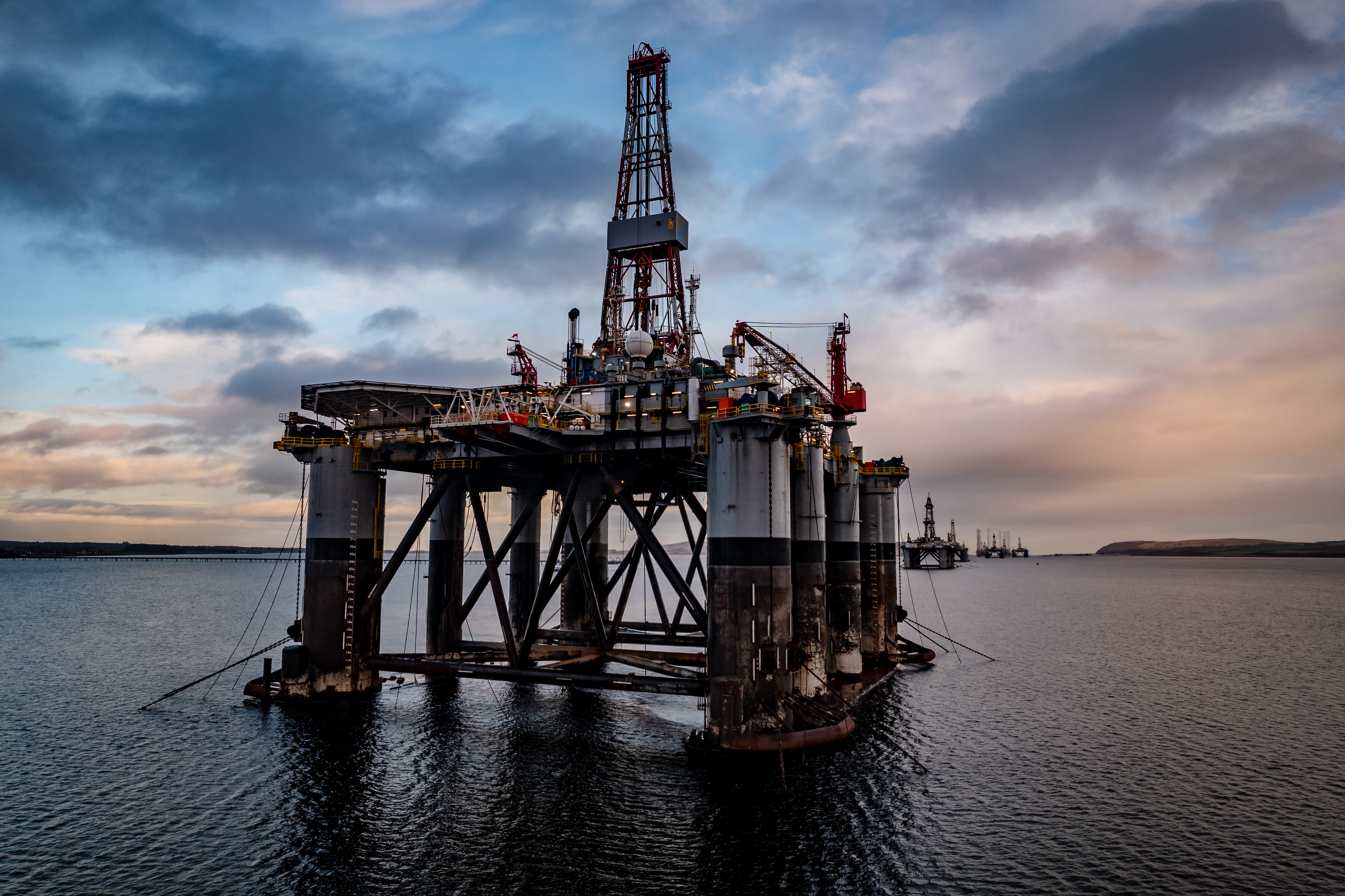
A Deeper Understanding of Pressure Transducers
Key Underwater Applications
Industrial Water and Wastewater Management
Pressure transducers are used to monitor water levels, pipeline pressure, and filtration systems, ensuring efficient and reliable operations. By providing real-time water level measurements, these sensors help prevent overflow and depletion and reduce blockages and pump inefficiencies.
Offshore Oil Drilling and Gas Exploration
Pressure transducers are essential for monitoring wellbore pressure, subsea pipelines, and blowout preventers, ensuring safety and operational efficiency in offshore drilling operations. They help detect pressure anomalies that could indicate leaks, blockages, or well control issues, allowing for early intervention and reduced downtime. These sensors provide real-time data that supports automated safety and regulatory compliance.
Hydroelectric Power Generation
Hydroelectric plants depend on pressure transducers for monitoring water flow and reservoir levels, optimizing energy production, and preventing structural failures. These sensors help regulate turbine efficiency by ensuring consistent water pressure, maximizing power output while reducing mechanical strain. Additionally, they play a crucial role in dam safety by detecting pressure fluctuations that could indicate leaks or structural weaknesses, enabling proactive maintenance and disaster prevention.DwyerOmega's submersible pressure transducers, such as the PX709GW Series, provide accurate pressure readings, enabling operators to optimize energy production and ensure the longevity of equipment.
Ballast and Fuel Management in Marine Vessels
Marine vessels rely on ballast and bilge systems to maintain stability and safety. The PX633 Series Submersible Pressure Transmitters monitor pressure levels in these systems, ensuring proper water displacement and preventing potential hazards associated with improper ballast or bilge operations. Their rugged stainless steel body and advanced sensor technology make them ideal for the harsh conditions encountered in marine environments.
Environmental Challenges and Performance Requirements
Pressure and Depth Considerations
One of the primary challenges in underwater applications is dealing with the increasing hydrostatic pressure exerted by water as depth increases. Every 10 meters of depth adds approximately 1 bar (14.5 psi) of pressure. Pressure transducers must be designed with appropriate depth ratings to ensure they operate effectively without structural failure or performance degradation.
Temperature Variations
Water temperatures can fluctuate significantly, especially in deep-sea environments where thermal gradients exist. These temperature changes can affect the accuracy and stability of pressure measurements, making temperature compensation a critical feature in transducer design.
Corrosion, Material Degradation, and Contamination
Seawater is highly corrosive, which can degrade standard materials over time. Pressure transducers used in marine environments must be constructed from corrosion-resistant materials such as stainless steel, titanium, or specialized coatings to ensure long-term durability and performance. In addition to corrosion, underwater sensors are also at risk of contamination from biofouling, which occurs when marine organisms such as algae and barnacles attach to the sensor surface, obstructing measurements and damaging components. The accumulation of sediment or debris can further compromise sensor accuracy. To mitigate these risks, pressure transducers are often designed with smooth, non-porous surfaces, and are treated with anti-fouling coatings, ensuring reliable function even in harsh, contamination-prone underwater conditions.
Key Design and Selection Considerations
Material Selection
The choice of materials for a pressure transducer impacts its durability and longevity in underwater conditions. Stainless steel is a common choice for shallow applications, while titanium offers superior corrosion resistance for deep-sea deployments
Sealing and Waterproofing
Proper sealing is essential to prevent water ingress, which can compromise sensor function. Hermetically sealed designs and robust cable entry points enhance the reliability of pressure transducers in submerged environments.
Depth Rating and Pressure Limits
Selecting a transducer with an appropriate depth rating ensures it can withstand the intended operating conditions. Manufacturers specify depth and pressure limits based on sensor design, and exceeding these limits can lead to measurement errors or device failure.
Signal Output and Integration
Underwater pressure transducers often provide analog (e.g., 4-20mA) or digital (e.g., RS-485) outputs. The choice of output type depends on the application’s data acquisition system and requirements for real-time monitoring and signal transmission over long distances.
Calibration, Maintenance, and Longevity in Underwater Applications
Calibration Needs
Regular calibration ensures that pressure transducers maintain their accuracy over time. In underwater applications, sensors may be calibrated before deployment and periodically verified using reference measurements or retrieval-based recalibration.
Maintenance Strategies
Proactive maintenance extends sensor lifespan and reliability. Cleaning, protective housing, and periodic inspections help prevent biofouling, corrosion, and mechanical wear, reducing the risk of sensor failure.
Failure Modes and Troubleshooting
Common failure modes include water ingress, signal drift, and material degradation. Understanding these issues and implementing diagnostic techniques, such as monitoring for irregular signal behavior, helps mitigate potential failures before they impact operations.
Emerging Trends in Underwater Pressure Transducers
Innovations in materials and sensor miniaturization are improving the durability and accuracy of underwater pressure transducers. New manufacturing techniques allow for more compact, efficient designs capable of withstanding extreme environments.
Advances in IIoT and wireless technology are enabling real-time data transmission from submerged sensors, reducing the need for physical retrieval and improving monitoring efficiency.
As underwater exploration and industrial activity continue to expand, pressure transducer technology will evolve to meet new demands. Enhanced durability, smarter sensing capabilities, and improved integration with autonomous underwater vehicles (AUVs) will shape the future of underwater pressure measurement.
By understanding the critical considerations and selecting the right products, industries can ensure their underwater operations remain efficient, accurate, and sustainable.
Contact Us Today!