Thermocouple wire is a temperature measurement conductor made from the same alloy materials as the thermocouple sensor itself. Its primary role is to extend the thermocouple circuit from the sensing junction to the instrument without introducing additional EMF (electromotive force) error.
Unlike standard copper or general-purpose extension wire, thermocouple wire must precisely match the thermoelectric properties of the specific thermocouple type — such as Type K, J, or T. This ensures the integrity of temperature measurements across the entire system, especially in industrial applications where precision is critical.
Shop for DwyerOmega Thermocouple Wire Here!
Thermocouple Wire Types and Temperature Ranges
Since thermocouple wire must maintain the same thermoelectric behavior as the sensor it connects to, different thermocouple types are defined by their specific metal pairings. Each pairing responds uniquely to temperature, influencing the wire’s accuracy, usable temperature range, and suitability for various environments. Understanding these differences is essential when selecting wire for precise and consistent measurements in industrial applications.
Comparing (Some) Thermocouple Wire Types
Type | Temperature Range | Sensitivity | Oxidation Resistance | Alloy Composition | Common Uses | |
---|---|---|---|---|---|---|
K | -200 °C to 1,260 °C | Medium | High | Chromel / Alumel | Industrial furnaces, engines, kilns | Buy Now |
J | -40 °C to 750 °C | High | Low | Iron / Constantan | Plastics processing, older equipment | Buy Now |
T | -200 °C to 350 °C | High | Excellent (moisture) | Copper / Constantan | Cryogenics, food processing | Buy Now |
N | -200 °C to 1,300 °C | Medium | Excellent | Nicrosil / Nisil | High-temp precision, harsh environments | Buy Now |
Insulation Types and Environmental Resistance
Thermocouple wire is available with a variety of insulation types, selected based on environmental conditions, temperature range, and chemical exposure:
Insulation Type | Key Characteristics |
---|---|
PVC | Economical, flexible, and moisture-resistant |
PFA | Offers excellent chemical resistance and high-temperature durability |
TFE | Chemically resistant and non-stick; up to 260 °C; ideal for corrosive or wet conditions |
FEP | Variant of PTFE with excellent dielectric strength and moisture resistance |
Fiberglass | Suitable for high-heat environments up to 482 °C; moderate chemical resistance |
The correct insulation protects both the wire and the signal from heat, abrasion, chemicals, and mechanical stress. For outdoor or rugged industrial applications, dual-jacketed and armored thermocouple wires may offer added protection.
Thermocouple Wire vs. Extension Cable
Although both thermocouple wire and extension cable serve to transmit temperature signals, they differ in material composition, purpose, and appropriate use cases.
-
Thermocouple Wire
Made from the exact same metal alloys as the thermocouple probe (e.g., Chromel/Alumel for Type K), thermocouple wire is designed to maintain signal accuracy from the measurement junction all the way to the instrumentation. It should be used anywhere precise temperature readings are critical, especially in the sensing zone.
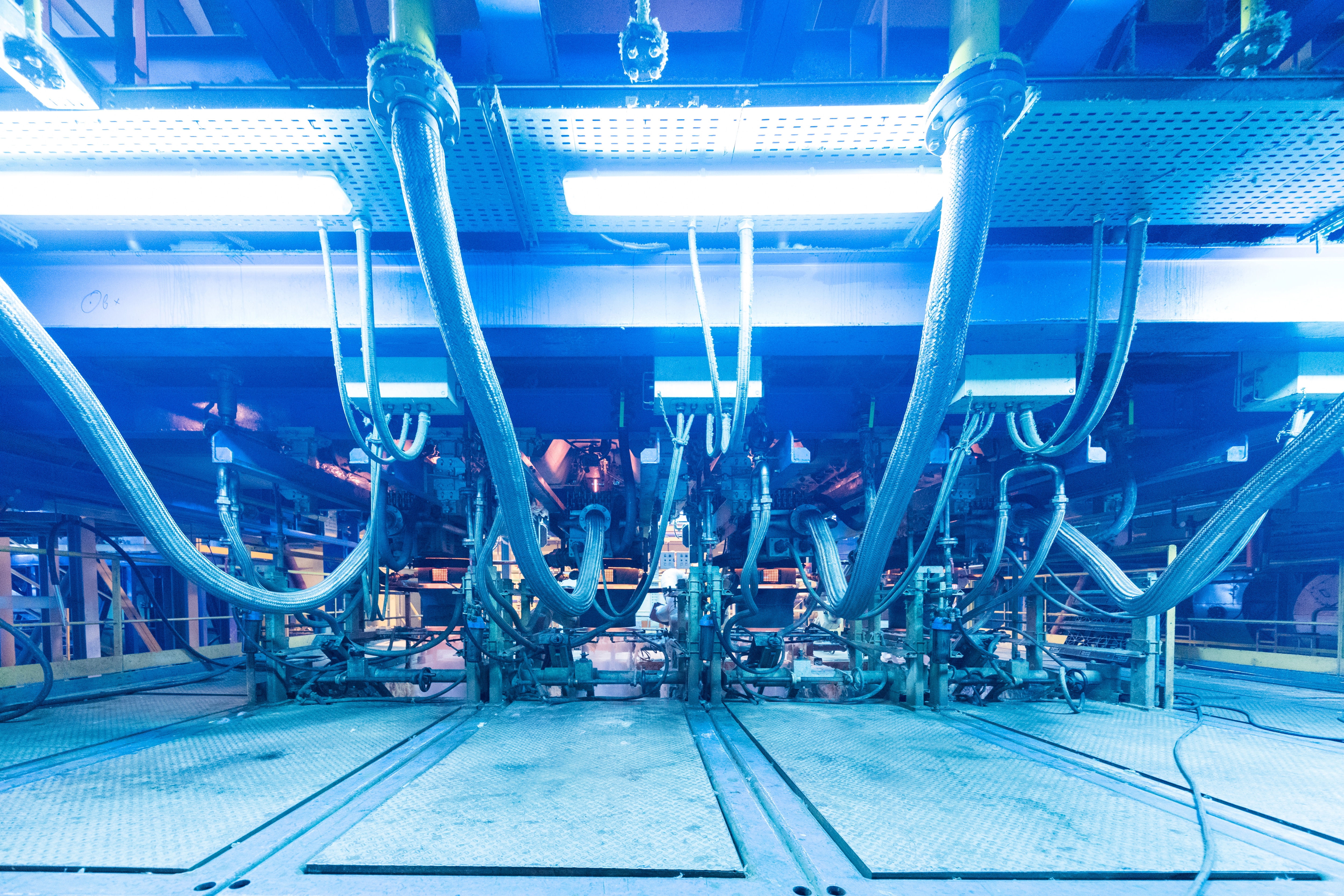
Extension Cable
Extension cable uses less expensive alloys that mimic the thermoelectric properties of the actual thermocouple type over a limited temperature range. It’s intended for extending the connection between the thermocouple and the readout device—but only in areas with minimal thermal gradient. Extension wire should never be used near the sensing point, as it may introduce error if exposed to significant temperature differences.
While extension wire may offer cost savings, it should only be used within specified limits and never in the sensing zone. For critical measurements—especially in high-temperature, high-vibration, or chemically aggressive environments—thermocouple wire ensures signal fidelity from the point of measurement to the instrumentation, maintaining the accuracy, repeatability, and reliability that industrial applications demand.
Best Practices for Thermocouple Wire Installation
Proper installation of thermocouple wire is essential to preserve measurement accuracy and ensure reliable long-term performance. Even the most precise thermocouple sensor can yield inaccurate readings if the wire is mishandled, incorrectly routed, or poorly terminated. The following best practices help maintain signal integrity and minimize sources of error:
-
Maintain Polarity
Thermocouple wires are polarity-sensitive. Always connect positive to positive and negative to negative—reversed polarity introduces significant measurement errors.
Use Matching Alloy Connectors
Terminate thermocouple wires using connectors made of the same thermocouple alloy. Avoid copper or dissimilar metal terminals, which can create unintended junctions and additional electromotive force (EMF).
Route Away from Electrical Noise
Install thermocouple wire away from high-voltage lines, motors, and other sources of electromagnetic interference (EMI). Use twisted-pair and/or shielded cable in electrically noisy environments and ensure proper grounding per instrumentation standards.
Avoid Mechanical Stress
Do not sharply bend, crush, or over-tighten thermocouple wire. Mechanical stress can alter wire characteristics, introduce resistance, and degrade long-term accuracy.
Minimize Junction Points
Keep splices and connections to a minimum. Every junction is a potential source of error unless thermoelectrically matched and properly insulated.
Protect from Heat and Contaminants
Use appropriate insulation materials based on temperature and environmental exposure. In high-temperature or corrosive environments, choose wire rated for those conditions to prevent degradation.
Perform Routine Calibration Checks
In cyclic or high-temperature applications, periodically verify the system’s accuracy against a known standard. Drift in thermocouple wire or junctions over time can compromise reliability.
Contact a DwyerOmega Expert Today!