A heat trace system is a critical solution for preventing process equipment (most commonly pipes, valves, and tanks) from freezing or losing heat in cold environments. Widely used in industrial facilities, commercial complexes, and at-home applications, these systems provide targeted thermal protection that helps ensure overall process reliability.
Why Use Heat Trace Systems?
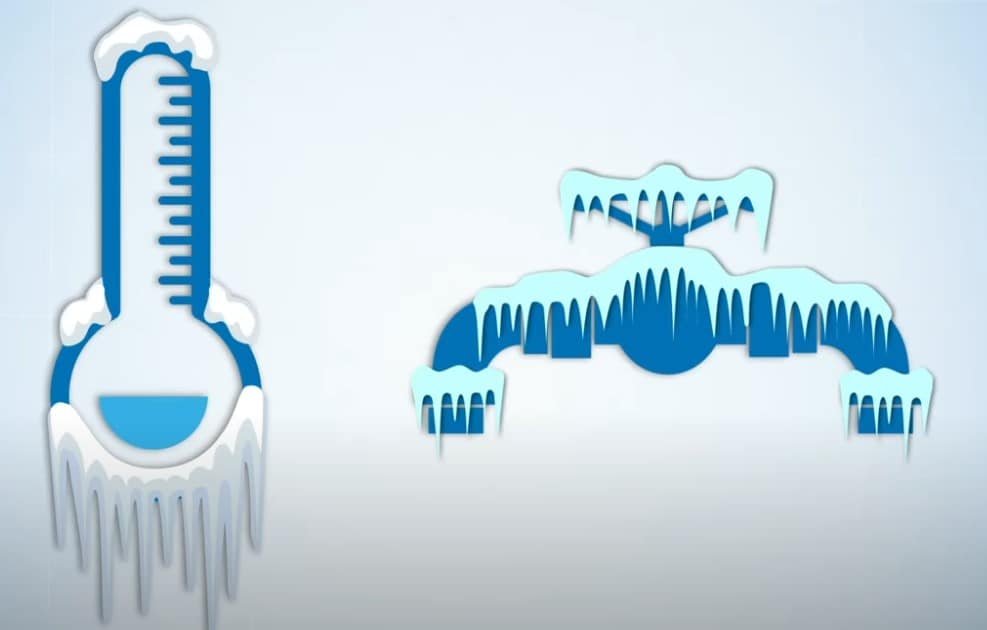
When temperatures drop, pipes carrying liquids are vulnerable to freezing. This can slow flow and change viscosity, causing pipes to crack and burst—leading to expensive repairs, property damage, and unplanned downtime.
A well-designed heat trace system not only prevents freeze-related failures, but it also maintains stable temperatures. In many industrial applications, even slight heat loss can disrupt flow rates or chemical reactions. Heat tracing ensures liquids stay at the right temperature, protecting product quality and keeping systems running smoothly.
How Does a Heat Trace System Work?
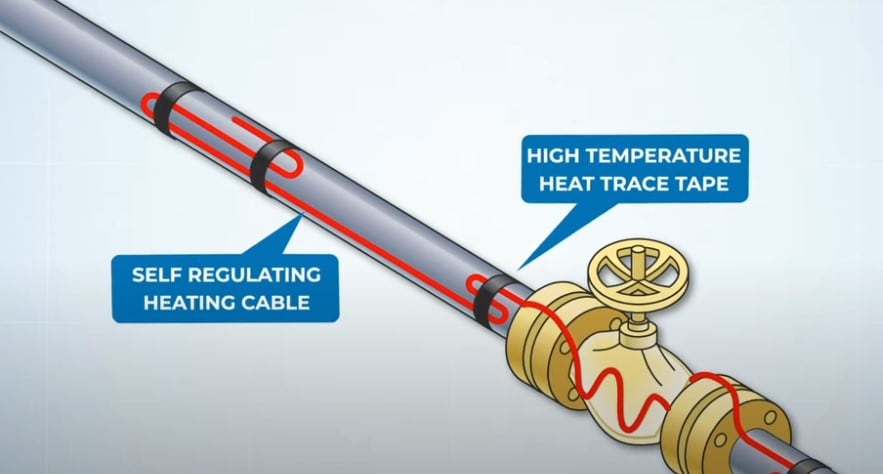
A heat trace system works by applying heat directly along the length of a pipe or vessel to prevent freezing or maintain a specific temperature. It starts with a heating cable that’s fastened snugly to the pipe using high-temperature heat trace tape. This cable is then powered through a dedicated connection, often a simple power connection box. For systems that demand tighter temperature control and accuracy, a digital thermostat can be used. It not only connects the cable to power but also continuously monitors and regulates the pipe temperature.
When there is a junction or branch in the piping that also needs heating, a multiple entry connection box can be used to split the heating cable run and extend coverage where it is needed. At the end of each heating cable run, end seals are installed to protect against moisture ingress and physical damage.
After the cables are in place, everything gets wrapped up in thermal insulation. This step dramatically reduces heat loss to the surrounding environment, boosting the energy efficiency of the whole setup. Finally, heat trace caution labels are applied on the outer surface of the insulation, spaced roughly every ten feet. These serve as clear warnings for maintenance personnel and emergency responders that electrical heating elements are at work underneath, and the surface may be hot.
Altogether, this is a straightforward but highly effective system for protecting pipes and ensuring process reliability—even in the coldest conditions.
Heat Trace Solutions from DwyerOmega
Self-Regulating Heating Cable
SRM/E Self-Regulating Heating Cables offer a safe, dependable solution for heat tracing applications—whether it’s maintaining process temperatures or protecting pipes, valves, and tanks from freezing. With a maximum exposure temperature of 190 °C (375 °F), these cables can even withstand steam cleaning of equipment using steam up to 170 psig. Designed for versatility, SRM/E cables are well-suited for hazardous environments and can also handle certain corrosive conditions, making them a robust choice for a wide range of industrial needs.
Key Features:
- 5, 10, & 20 Watts/ft
- 120 and 240V options
- 150 °C (302 °F) Maximum Maintenance Temperature
- Energy Efficient
Digital Heat Trace Controller and Digital Thermostat
The ITC and DTS Digital Heat Trace Controller and Digital Thermostats are designed for peak performance and control. Their intended function is to properly control heating cable for freeze protection or maintaining process temperatures of pipes or other equipment. The Soft Start feature removes in-rush current that self-regulating cables cause, this feature eliminates tripped circuits especially for colder temperatures. Hazardous Area apporvals allows these units to be used in many environments.
Key Features:
- High resolution display (ITC Models)
- Touch control (ITC Models)
- RTD sensor included (DTS Model Only)
- Rated for hazardous and non-hazardous areas
Heat Trace Power Connection, End Seal, and Splice Kits
HT-KIT Heat Trace Power Connection, End Seal, and Splice Kits are utilized so the user can connect power supplies to the heat trace products (UMC & UPC) and provide end sealing (UES & UESL) for the heating cable to terminate the cable connections. These connections kits are designed so that no matter the environment they can delivery outstanding performance in non-hazardous and harzardous locations. The difference between the UMC and UPC is that the UMC power connection kit can connect mulitple circuits in one box while the UPC is design for only one circuit. The difference between the UES and UESL is that the UESL has a light to provide indication that power is making it all the way through the cable. RTST allows the user to splice or tee heating cable to extend the connection to additional piping or equipment.
Key Features
- UMC & UPC are power connection boxes to connect external power to heat trace cable
- UES & UESL are end seals for heat trace cable but only the UESL has an indication light
- NEMA 4X enclosure for complete safety
- Non-flammable
Connect with a DwyerOmega Expert Today!